Automated Quality Control with AI in Cement Industry
A Vision Solution by Irida Labs and Basler
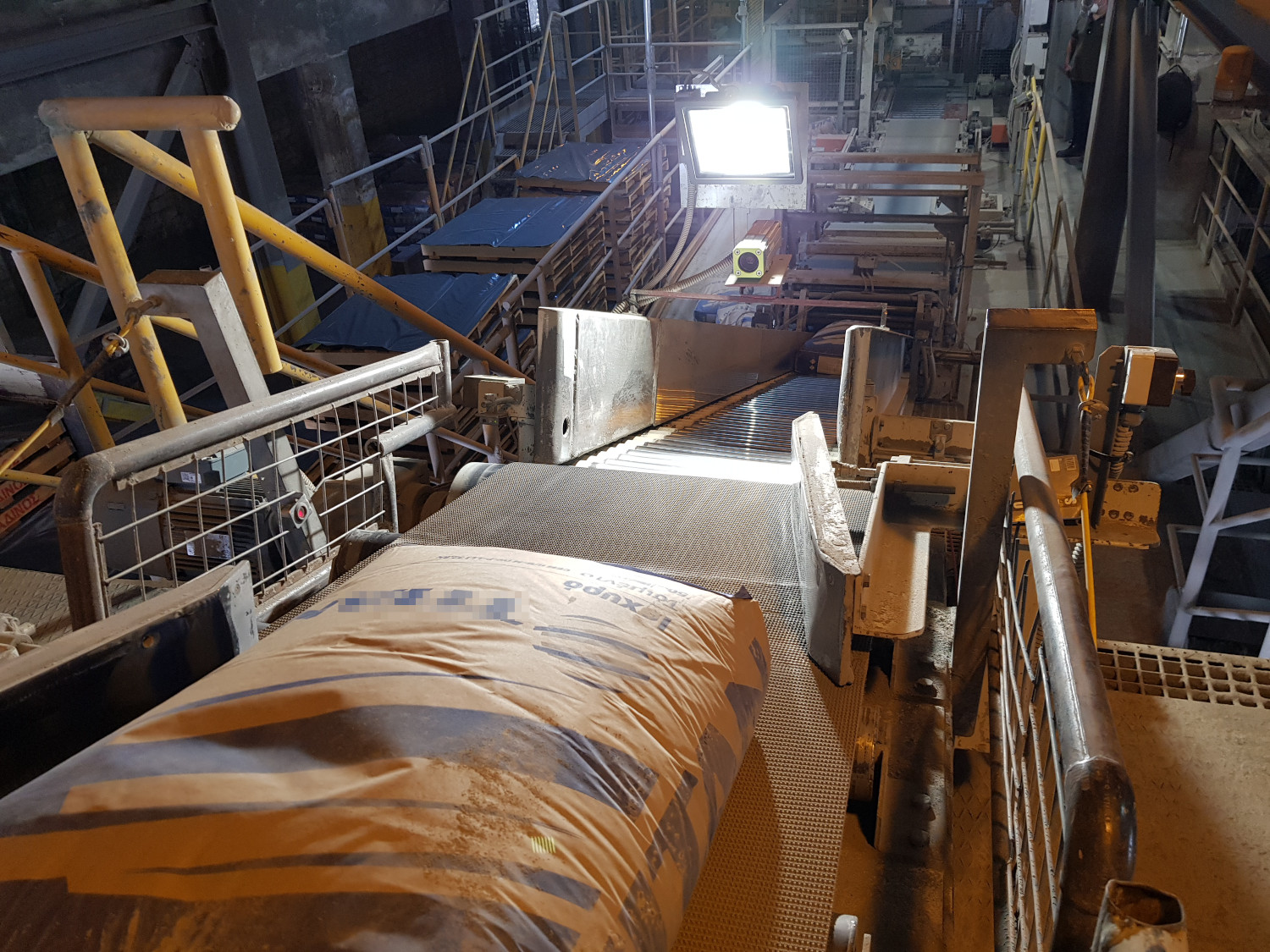
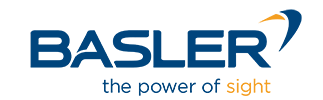
Cement Industry Production: A Fast-Pacing, Harsh Environment
Cement industry provides an example of heavy industrial manufacturing process, involving multiple, complex stages before the end-product gets ready for shipping. A typical cement plant has a production capacity of several thousand tons per day, which is translated to a continues output of tens (or hundreds) of bags per minute on a 24/7 basis.
In such a fast-pacing production line, every halt (i.e. to remove a defective bag) is translated to a significant delay in the production, packaging and loading flow, which in turn impacts the overall efficiency and productivity KPIs. On the other hand, every undetected defective cement bag risks contaminating an entire pallet, not to mention hurting client relations and adding an excessive cost for returns, insurance or reimbursement. On top of the above, due to cement’s nature as a chemical product, legislation dictates very specific labelling requirements related to chemical, environmental and other specifications; failing to comply (due to printing or other failure) can lead to legal or financial consequences.
QA/QC Challenges for the Cement Industry
In order meet top-quality standards, this leading European cement manufacturer utilized human inspector shifts to perform a 24/7 in-line visual inspection on the produced cement bags.
The purpose of the project was to introduce a real-time quality inspection solution on cement bags that could identify any defects in random locations on the product’s surface, such as cracks, spills, dents, cuts, damaged edges or even printing failures. The solution should provide always-on defect detection on continuously running conveyor belts, while providing real-time alerts when a defective product is detected. Integration with (pre-existing or new) 3rd party systems should also be available, in order to handle these alerts and trigger specific actions (i.e. alarm, PCB, automated disposal etc), not to mention the collection of production analytics and statistics.
Last, but not least, the system should be robust against changing lighting conditions, excessive dust & dirt, vibrations, while being able to adjust to various packaging types (cement bags of different sizes and colours).
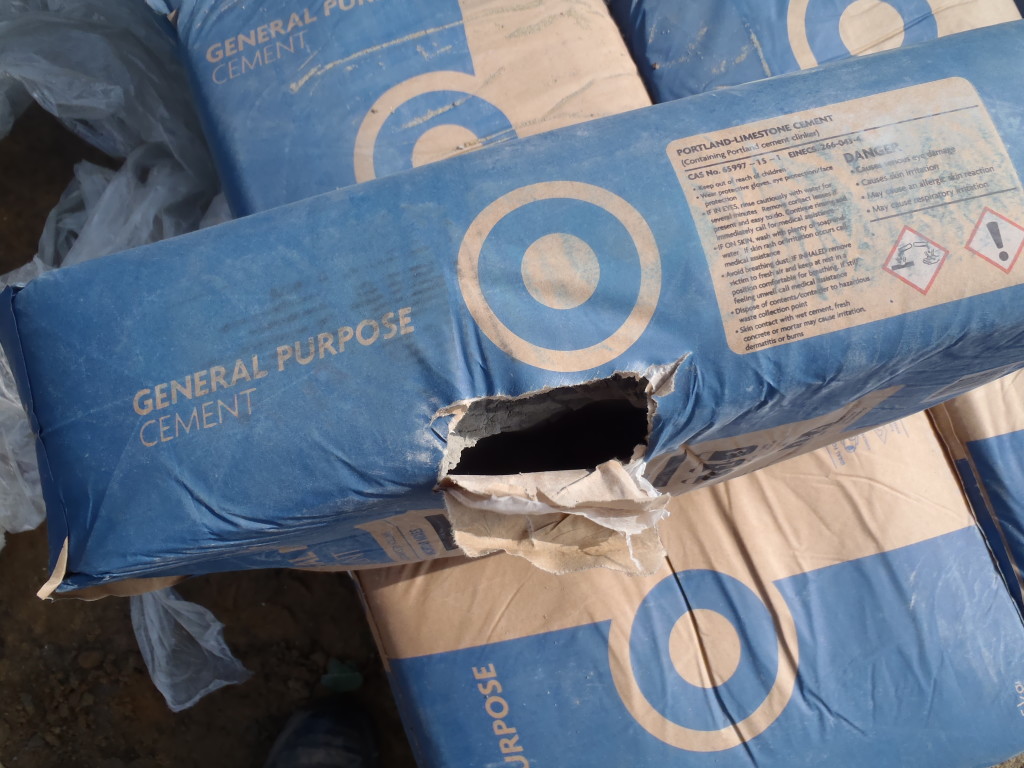
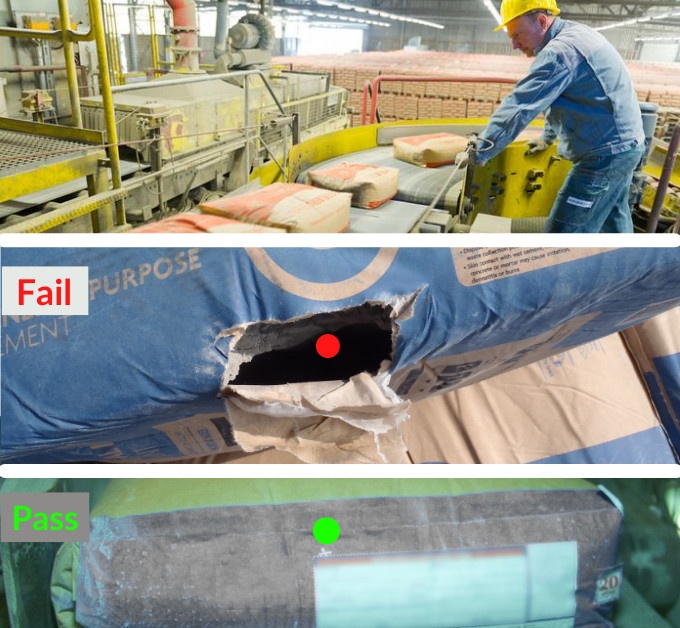
Human Visual Inspection
At its previous state, the packaged products Quality Control and Quality Assurance was performed via human visual inspection. This used to be a labour-intense process, involving 3 shifts of experienced operators to continuously oversee the production output, manually pause the conveyor systems in case of a detected defect, manually remove the defective bag and restore the operation. This process was highly prone to human errors, human fatigue even optical illusions, not to mention the sub-optimal efficiency and output due to the inevitable delays. Trustworthy data collection regarding the defects was also insufficient, making QA/QC process non-measurable and thus harder to improve.
Artificial Intelligence is the game changer in this area, introducing next generation Industry 4.0 Vision AIoT solutions , allowing numerous Smart Factory applications. Specifically on the QA/QC, Vision AI surpasses human vision in quality and quantity measurements because of its speed, accuracy, repeatability and scalability. Combined with the necessary optics, Vision AI can also detect defects that are impossible to consistently spot with the naked eye!
The Computer Vision & AI Packaging Integrity & QA Solution
The implemented Computer Vision & AI Packaging Integrity & QA solution is based on PerCV.ai and offers full automation in the Quality Assurance and Quality Control processes.
On the ground, each camera sensor for the Edge Vision AI Solution is paired with an on-premises processing device that operates as near as possible to the sensor. Each sensor is positioned at the optimal distance/height/angle indicated by Vision System Design, so the products are within its field of view and the characteristics-to-be-monitored are visible (aka 5 out of 6 sides of each product). The Vision AI solution is comprised of the following components:
PerCV.ai Vision AI Software & Services Platform
The solution is powered by PerCV.ai, Irida Labs’ end-to-end software & services platform for deploying Vision AI at scale. PerCV.ai handles the heavy lifting of orchestrating all the building blocks required to deploy a Vision AI solution; Vision Sensors & Edge Devices, Digital Vision Twin, Edge Hardware, Vision AI Software, Data Engine, APIs and AI Analytics are all integrated into the platform, streamlining development to support of both POC as well as full-scale production.
Components of the Vision AI Solution
Fully custom Vision AI software, tailored to each plant production specifics. Under the hood, PerCV.ai platform for on-device Vision Intelligence is utilized to build efficient and robust Defect Detection, Packaging Integrity and Quality Assurance solutions, that run in real-time and rely solely on our proprietary ML engine. With the use of state-of-the-Art Vision AI algorithms, it is capable of identifying spills, dents, cuts, damaged edges, even printing failures with over 99.9% accuracy, while continuously learning and adjusting on new types of defects and products.
The host device is an Edge Device or Industrial PC utilizing an AI accelerator (such as ADLINK NVIDIA® Jetson Nano™ Edge Inference Platform), being able to provide the sensor with the computational power required to run advanced AI vision workloads.
Dashboard & AI Analytics are powered by PerCV.ai providing real-time visual check of the functionality of the system. All metadata can also be transmitted to pre-existing software stack (i.e. ERP, WMS etc.) via the industry standard MQTT or HTTP protocols.
Basler ace series cameras (2 USB color cameras for defect detection and 1 Gige monochrome camera for printing failure checks) along with appropriate lenses are mounted on rigid brackets over the production line, triggered by a photocell for capturing the cement bags at the same time, therefore being able to inspect all bag sides on the same conveyor belt spot.
Camera module and optics are protected from the industrial environmental conditions (vibrations, dust, moisture) with a compact IP66/IP67 camera enclosure.

Get in Touch with our Team!
Explore further how our Vision AI Solution for Packaging Integrity & QA, powered by PerCV.ai, can help automate the integrity inspection and quality assurance procedures at your company.
We would love you to give us a very brief description of your implementation scenario, so that we assemble the most qualified team of Vision AI experts for our discussions!
Benefit of Using Vision AI in the Defect Detection System
It’s been over one year since the Vision AI Packaging Integrity & QA solution has been operational at the production line of TITAN. During this time, the company reports some remarkable results:
Zero-Defect Palletizing
The 24/7 automated unsupervised alerting on defects that require immediate attention/action constitute an immediate added value to the company, contributing to 95% reduction of defective bags being palletized as well as reduced Cost of Poor Quality (COPQ). Operations managers have a full overview of entire production process, in a single or even multiple sites, and they can react in real-time if/when needed.
Zero Returns
As an immediate consequence, the solution contributes to Zero Returns, since no defective products get palletized and get shipped to clients.
Labour Cost Reduction
80% Reduction in Labour Cost, since the solution eliminates the need for a manual human inspection of cement bags.
Compliance
Compliance with local / EU / International Regulations (label/date misprint), reduced regulatory fines risk
Efficiency in Production Processes
The system provides a real-time output when a defect is detected, which can in-turn trigger rejection systems, alarms or other automations. Detailed production analytics are being collected at the same time, providing an overview of the production output. All critical KPIs of the cement manufacturing process, including cement bag counting, defects detection (spills, dents, cut or damaged edges), printing failures (missing stamps, production date), are gathered in a single dashboard, allowing the real-time overview of one or multiple production lines from anywhere in the plant.
- Automatic, concurrent image capturing based on camera triggering mechanism
- Capture data / images during system operation and store to the local Industrial PC
- Visually check the Defect (or Production Date) that the AI system detected in real-time
- Data analytics and graph-based statistics (plots)
Get in Touch
Explore how our Vision AI solution can help automate the integrity inspection and quality assurance procedures at your company.
Industry Brief
In this Cement Industry Brief we present how Irida Labs’ PerCV.ai platform for on-device Vision Intelligence is utilized to build efficient, robust and scalable Industry 4.0 solutions for Cement Bags Identification & QA in conveyor belt systems that run in real time and rely solely on our proprietary ML engine.